Beer CO2 Pressure: Optimal Settings for Perfect Carbonation
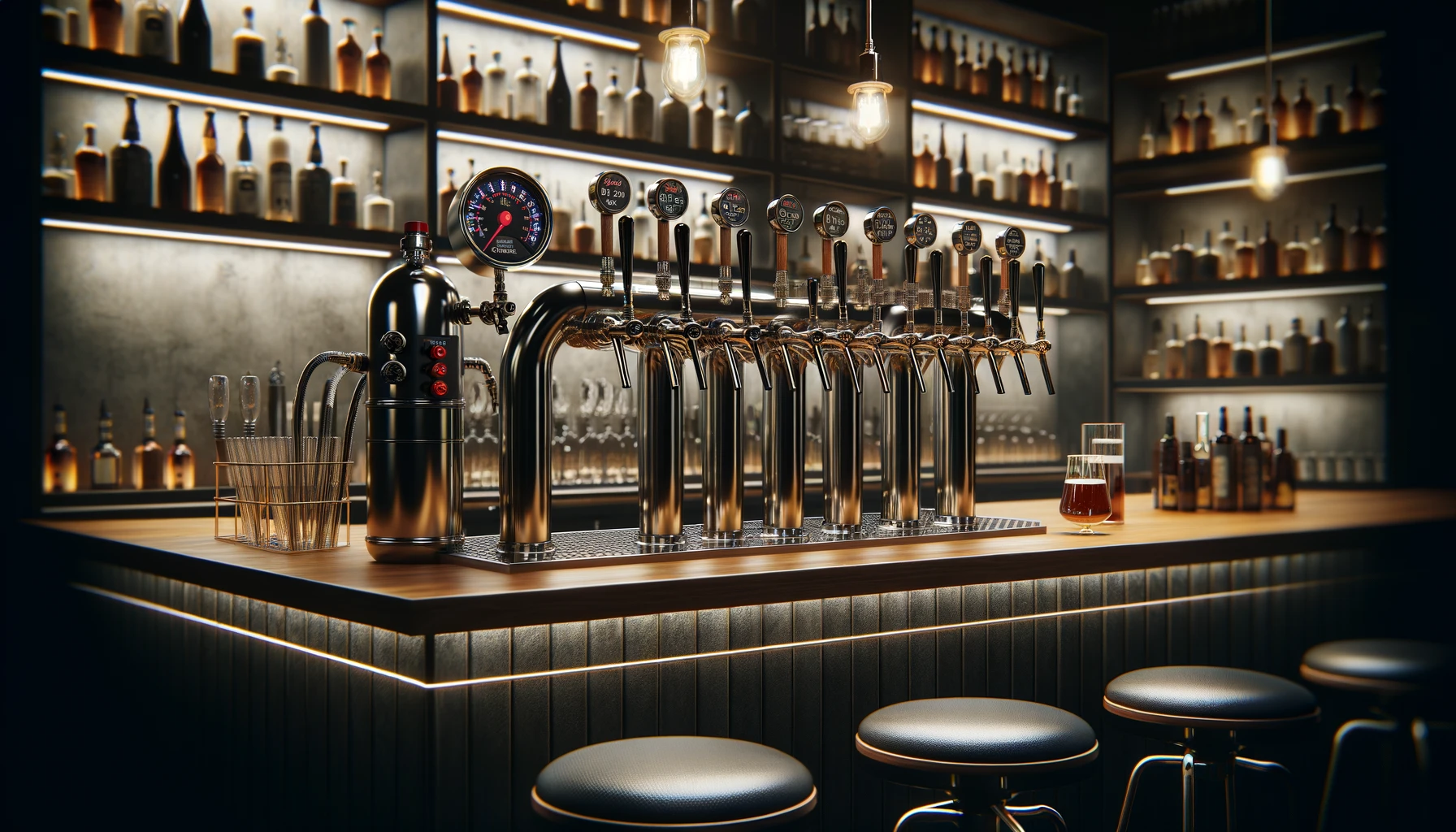
Carbonation is a critical component in the world of draft beer, giving the beverage its distinctive mouthfeel. It is achieved through a careful balancing act involving the beer carbonated with dioxide (CO2) under pressure. The right CO2 pressure is essential not only for maintaining the carbonation level desired for each beer style but also for ensuring the beer is delivered from keg to glass in optimal condition. Different beer styles may demand varying levels of carbonation, which is measured in volumes of CO2 and maintained through pressure settings in pounds per square inch (PSI).
Managing CO2 pressure in a draft system involves a combination of the right equipment and techniques. A kegerator or draft system is typically set up with a regulator that controls the flow of CO2 from the tank into the keg. The pressure setting must be adjusted according to factors such as beer style, temperature, and the desired amount of carbonation. Consistent monitoring and adjustments are vital to preserve the quality and flavor of the beer, as fluctuations in pressure can lead to under or over-carbonated beer. Safety is also a paramount concern, as CO2 is a pressurized gas, and proper handling and maintenance are required to prevent hazards.
Key Takeaways
- Appropriate CO2 pressure is vital for beer carbonation and delivery.
- Pressure settings vary with beer style, temperature, and desired carbonation.
- Regular monitoring and safe handling of CO2 are essential for system maintenance.
Understanding CO2 and Carbonation
Carbon dioxide (CO2) is the critical gas responsible for carbonation, influencing the texture, mouthfeel, and taste of a beer. To aim for a specific sensory experience, it's essential to control the volumes of CO2 in the brewing process.
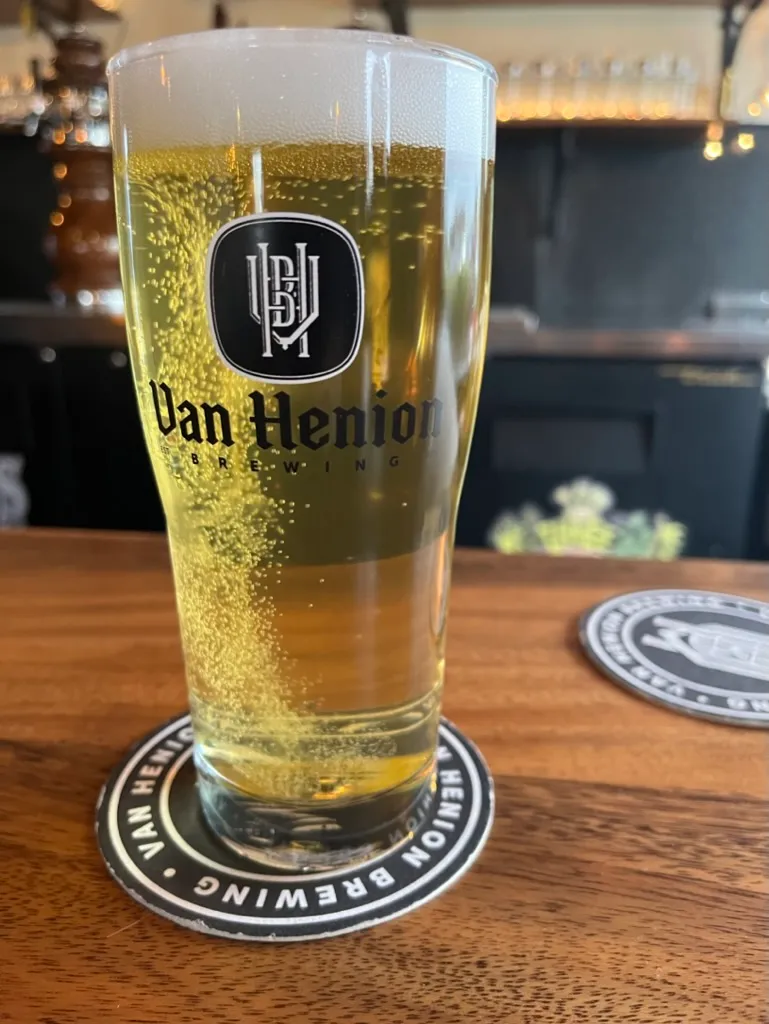
The Role of CO2 in Carbonation
Carbon dioxide is naturally produced during fermentation and can also be added externally to achieve the desired carbonation level of foamy beer. Proper carbonation will enhance the beer's aromatics and contribute to the drinkability of the style being served. The volumes of CO2 desired in a beer vary depending on its style; typically, light lagers might have higher carbonation levels with more volumes of CO2, while stouts often have lower levels.
When assessing carbonation needs, brewers refer to the desired carbonation levels, which are expressed in terms of volumes of CO2. This quantifies how many times the volume of CO2 if contained at atmospheric pressure, would fit into the same volume of liquid. The adept application of CO2 pressure can manipulate these levels to reach the desired carbonation level, ensuring the final outcome is both pleasurable and true to the intended style.
Beer CO2 Pressure Basics
The carbonation level in beer is maintained through precise CO2 pressure, typically measured in pounds per square inch (PSI). Ensuring the right CO2 pressure is vital for the optimal taste and presentation of different beer styles.
Ideal CO2 Pressure Ranges
Beer dispensing at an ideal pressure serves two functions: it maintains the beer's level of carbonation and propels the beer from the keg through the tap. Most beers perform well at a CO2 pressure between 12 to 14 PSI. Slight adjustments within this range can enhance the mouthfeel and flavor profile. However, every draft system has its own resistance or "restrictive value," so the ideal pressure may need to be tailored to fit specific setups.
CO2 Pressure for Different Beer Styles
Different beer styles require distinct pressures for an accurate representation of their intended flavor and carbonation levels.
- Ales, Ambers, and Pale Ales: Generally dispensed at 10-12 PSI to preserve their balanced carbonation.
- IPAs and American Sours: Can benefit from a similar range, 10-12 PSI, highlighting their characteristic hop profile and tartness without overcarbonation.
- Lagers, Pilsners, and Wheat Beers: Often served at a slightly higher pressure, around 12-14 PSI, to accentuate their crispness and fresh flavors.
- Stouts and Belgian Beers: Typically poured at a lower pressure, 8-10 PSI is common, as excessive carbonation can mask their complex flavors.
Note: These pressure ranges are not definitive and should be adjusted considering factors like temperature and your dispensing draft beer system's resistance. For example, a chart for determining the right pressure for your draft beer system may offer additional guidance. Adjustments might also be based on the desired carbonation level, which varies among different styles of beer.
For an accurate pressure setting, always consider the unique properties of the beer and the system it's being poured from.
Equipment and Setup
Setting up a draft beer system necessitates specific equipment to ensure a seamless and quality pour. Key components include a method to maintain and regulate pressure, storage for the beer, a delivery system, and a dispensing mechanism. Understanding each piece of equipment's role is crucial for both optimal performance and the longevity of the system.
CO2 Tanks and Pressure Regulators
CO2 tanks store carbon dioxide under high pressure, providing the force needed to move beer from the keg to the faucet. Pressure regulators are essential for controlling the output pressure from the CO2 tank dispensing keg, ensuring a consistent pour and proper carbonation levels. A typical CO2 regulator consists of gauges to monitor tank pressure and the pressure applied to the keg.
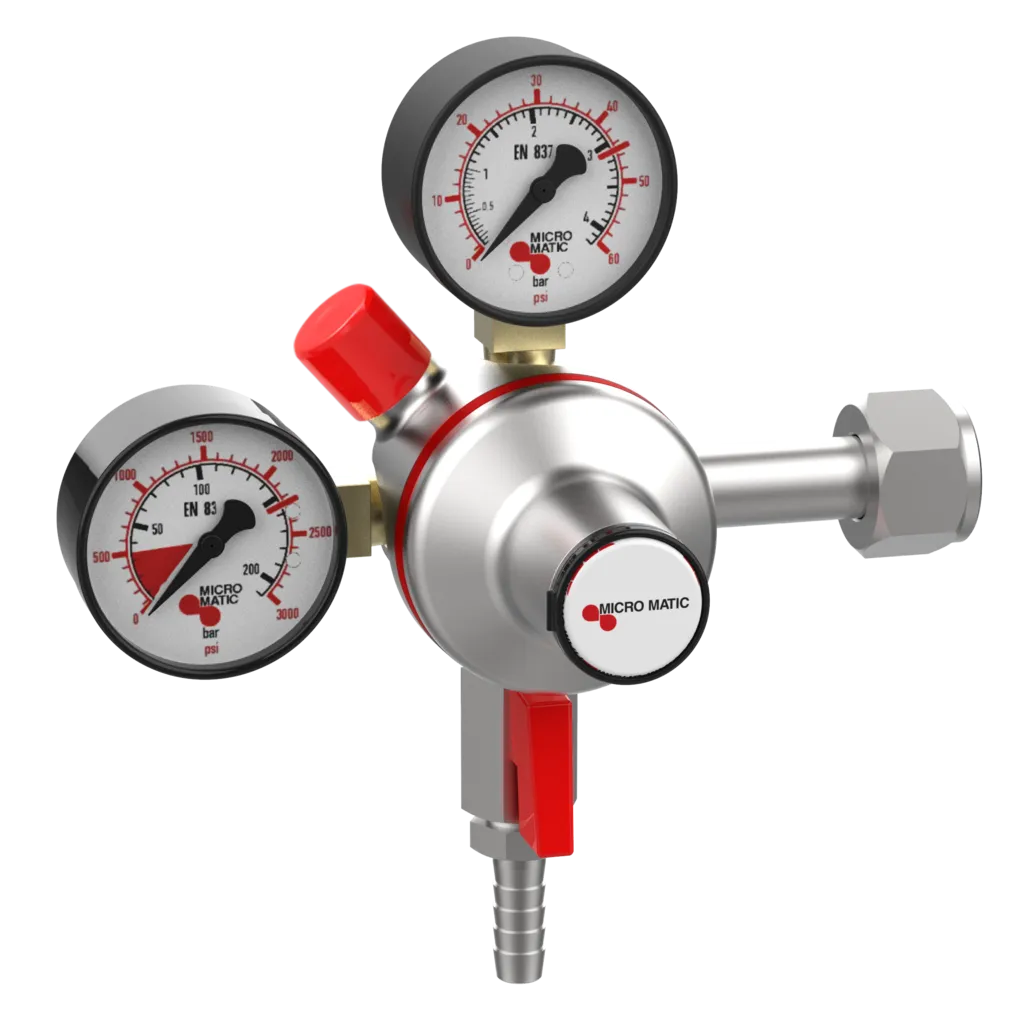
Kegerators and Kegs
Kegerators are specialized refrigerators designed to house one or more kegs of beer. They not only keep the beer chilled but also provide a platform to integrate taps and CO2 systems seamlessly. Kegs themselves are usually made of stainless steel, designed to contain and preserve the flavor and quality of the draft beer.
Beer Lines and Taps
Beer lines, typically made from vinyl or stainless steel, connect the keg to the tap or faucet where the beer is dispensed and served. The line's cleanliness and material can affect the beer's taste and longevity. Faucets handle the final dispense of the beer, and having a high-quality tap can reduce excess foam and ensure a smooth pour.
Long-Draw Draft Beer Systems
Long-draw systems are used when there is a considerable distance between the keg storage and the pouring location. These setups generally utilize a combination of CO2 and nitrogen to propel the beer through a longer beer line without overcarbonating it. Such systems require precise regulator pressure settings to balance the mixed beer gas proportions and maintain the correct pressure throughout the line.
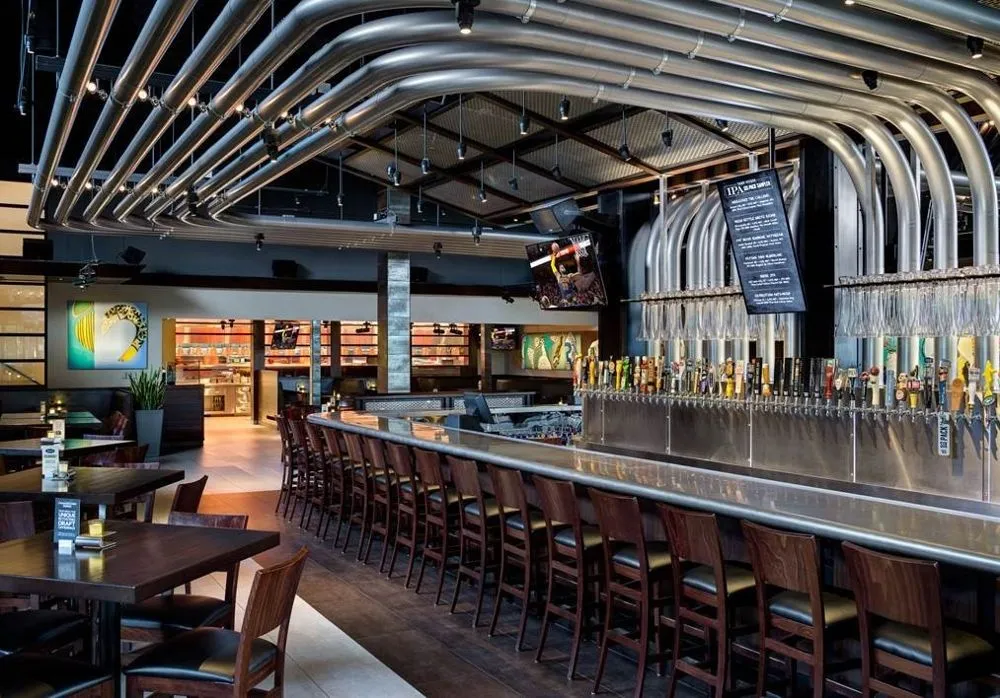
Direct Draw Beer Systems
Direct-draw keg beer can systems are typically used in smaller bars or at home where the keg and kegerator are in close proximity to the tap. This setup minimizes the length of the beer line needed, reducing the potential for temperature fluctuations and simplifying maintenance. Direct draw systems are cost-effective and easier to install, making them a popular choice for casual or non-commercial users.

Carbonation Techniques
In the world of homebrewing, carbonation is imperative for achieving the desired fizziness and mouthfeel of beer. Specific methods and equipment adjustments ensure that brewers can control the level of carbonation precisely.
Force Carbonation
Force carbonation is a commonly employed method by homebrewers to carbonate their beer quickly and efficiently. By sealing beer within a keg and adding carbon dioxide under pressure, it dissolves into the liquid, which results in carbonated beer. The process involves using a CO2 tank connected to a pressure gauge that allows precise control over the amount of gas infused into the beer. Typically, keg temperature plays a critical role in force carbonation; colder temperatures allow for faster absorption of CO2.
Pressure Adjustments for Serving
Once beer is carbonated, serving it at the right pressure is crucial to maintain the perfect level of carbonation. This involves adjusting the pressure on the keg’s CO2 tank using a pressure gauge. The goal is to find a balance between preserving the beer's carbonation and preventing excessive foaming. Homebrewers can refer to a carbonation table or keg pressure chart for guidance on setting proper pressures based on keg temperature. Additionally, the type of serving setup, such as a picnic tap or a full kegerator system, will determine the required pressure adjustments to ensure that force carbonated beer retains its quality during serving.
CO2 Pressure Management
Managing CO2 pressure in the head space a draft beer system is crucial for maintaining the beer’s carbonation at optimal levels. It hinges on a proper understanding of the science behind carbonation and the mechanical aspects of draft systems.
Finding the Right Balance
The right CO2 pressure is essential to serve beer with the perfect amount of carbonation and head. Beer should be dispensed at a psi level that aligns with its style and keg temperature. Typically, ales and lagers have a recommended CO2 pressure of 10-12 PSI at a temperature of 38 degrees Fahrenheit. Adjusting the beer regulator and setting precisely is imperative to avoid under-carbonation or over-carbonation. Under-carbonated beer can taste flat, whereas over-carbonated beer may become excessively foamy, leading to unnecessary waste.
Troubleshooting Common Issues
When encountering issues such as foamy pours or beer that has too much foam and little head, one might need to assess several factors:
- Low pressure may result in a flat beer with an inadequate head. Inspect the regulator setting and increase the psi incrementally to correct this issue.
- Conversely, higher pressure can cause over-carbonation, which often leads to a glass full of foam. To fix this, the pressure relief valve can be used to release excess pressure.
- The line length and gravity also play roles in balancing line resistance and pressure. A system with too much line resistance might require a bit more CO2 pressure, while too little resistance could prompt a decrease in psi.
- Consistent temperature is key; fluctuating keg temperatures can cause pressure issues, leading to under or over-carbonating. Maintain a steady keg temperature for consistent results.
- Regularly check for leaks and faulty equipment, such as damaged relief valves or pressure relief valves, which could disrupt CO2 pressure accuracy.
By diligently monitoring these elements and implementing proper troubleshooting procedures, one can manage CO2 levels effectively, ensuring each beer is presented at its best.
Advanced Considerations
In the pursuit of the perfect draft, considerations such as altitude have significant implications on carbonation levels and pressure settings.
Altitude's Effect on CO2 Pressure
One's elevation above sea level directly influences the CO2 pressure required to maintain optimal carbonation in beer. At higher altitudes, the atmospheric pressure is lower; thus, lower CO2 pressure is needed compared to sea level settings to achieve the same level of carbonation in beer. Long-draw draft beer systems that run over greater distances, particularly in elevated locations, must account for this reduction in external pressure.
A table showcasing general pressure adjustments for various altitudes:
Altitude (feet) CO2 Pressure Adjustment (PSI) 0 - 2,000 0 - 1 (increase) 2,001 - 4,000 1 - 2 (decrease) 4,001 - 6,000 2 - 3 (decrease) 6,001+ 3+ (decrease)
The length of the beer line also plays a critical role as resistance within the stainless steel beer lines themselves must be balanced with CO2 pressure to ensure a proper pour without excessive foam. Long-draw systems, especially those implemented at higher altitudes, require a precise calibration of CO2 pressure responsive to both distance and elevation to maintain the integrity of the beer's carbonation level.
Maintenance and Safety
Ensuring the integrity of a beer dispensing system involves regular scrutiny of equipment and adherence to rigorous safety protocols. These measures are critical in preventing accidents and maintaining the quality of the beer served.
Regular Equipment Checks
Maintenance is vital to the longevity and proper function of a beer CO2 system. One should perform inspections at scheduled intervals to ensure all components, including relief valves and pressure release valves, are in optimal condition.
- Weekly: Check all lines for signs of wear or leakage.
- Monthly: Verify that pressure release valves are operational to prevent over-pressurization.
- Bi-annually: Service the CO2 tank and regulator to ensure accurate pressure readings and delivery.
Safety Precautions
When handling CO2 systems, safety is of paramount importance. The pressurized nature of the gas source these systems can pose serious risks if not managed correctly.
- Always ensure the pressure release valve is functioning properly to avoid the risk of explosion due to overpressure.
- Wear protective gear when necessary, especially when connecting or disconnecting CO2 tanks.
- Store CO2 cylinders upright and secure them to prevent tipping and potential injury.
By strictly adhering to maintenance schedules and safety measures, operators can avoid hazardous situations and ensure the CO2 system functions correctly for consistent beer quality.
Frequently Asked Questions
Setting the correct CO2 pressure in a kegerator system is crucial for achieving the perfect pour and maintaining the quality of the beer. The following subsections address common queries and provide specific guidelines.
How do I correctly set the CO2 pressure for my kegerator system to ensure proper beer dispensing?
For optimal beer dispensing, the CO2 pressure should typically range between 12-14 PSI. However, factors such as the brewing industry, beer style, storage temperature, and elevation must be considered.
What is the ideal CO2 pressure to use for carbonating different types of beer?
Different beer styles require varying CO2 pressures for ideal carbonation. For example, wheat beers, Belgians, and sours require higher pressures. Assessing the ideal pressure for each style is essential for proper dispensing.
Can you provide a chart or guidelines for CO2 beer gas pressures specific to various beer styles?
While a precise chart is not provided here, general parameters suggest that lagers function well at lower pressures, while ales and stouts might need slightly higher settings.
What are the consequences of setting the CO2 pressure too high or too low in a beer keg?
Setting the CO2 pressure too high can lead to over-carbonation, resulting in foamy pours, while either too much pressure or low pressure might cause flat beer. Both scenarios adversely affect the taste and mouthfeel of the beer.
Summary
The correct CO2 pressure is crucial for serving and carbonating beer. Typically, a pressure between 12-14 PSI (pounds per square inch) is recommended for most ales and lagers at 38°F. It ensures the right level of carbonation without causing excessive foam or flatness.
Carbonation Methods:
- Slow-Forced Carbonation involves setting the regulator at a specific pressure and refrigerating the beer for several days.
- Burst Carbonation allows for faster carbonation by setting a higher PSI for a short period.
Key Points:
- Temperature influences the CO2 solubility in beer; colder beer can dissolve more CO2.
- Carbonation level is expressed in "volumes," indicating how many times the liquid volume of CO2 is dissolved in the beer.
- A straightforward guide can be found on using a carbonation table pressure chart to help brewers find the right balance. Accurate carbonation ensures the desired taste and mouthfeel of beer are achieved, thus enhancing the drinking experience.