Beer Line Size: Selecting the Optimal Diameter for Your Draft System
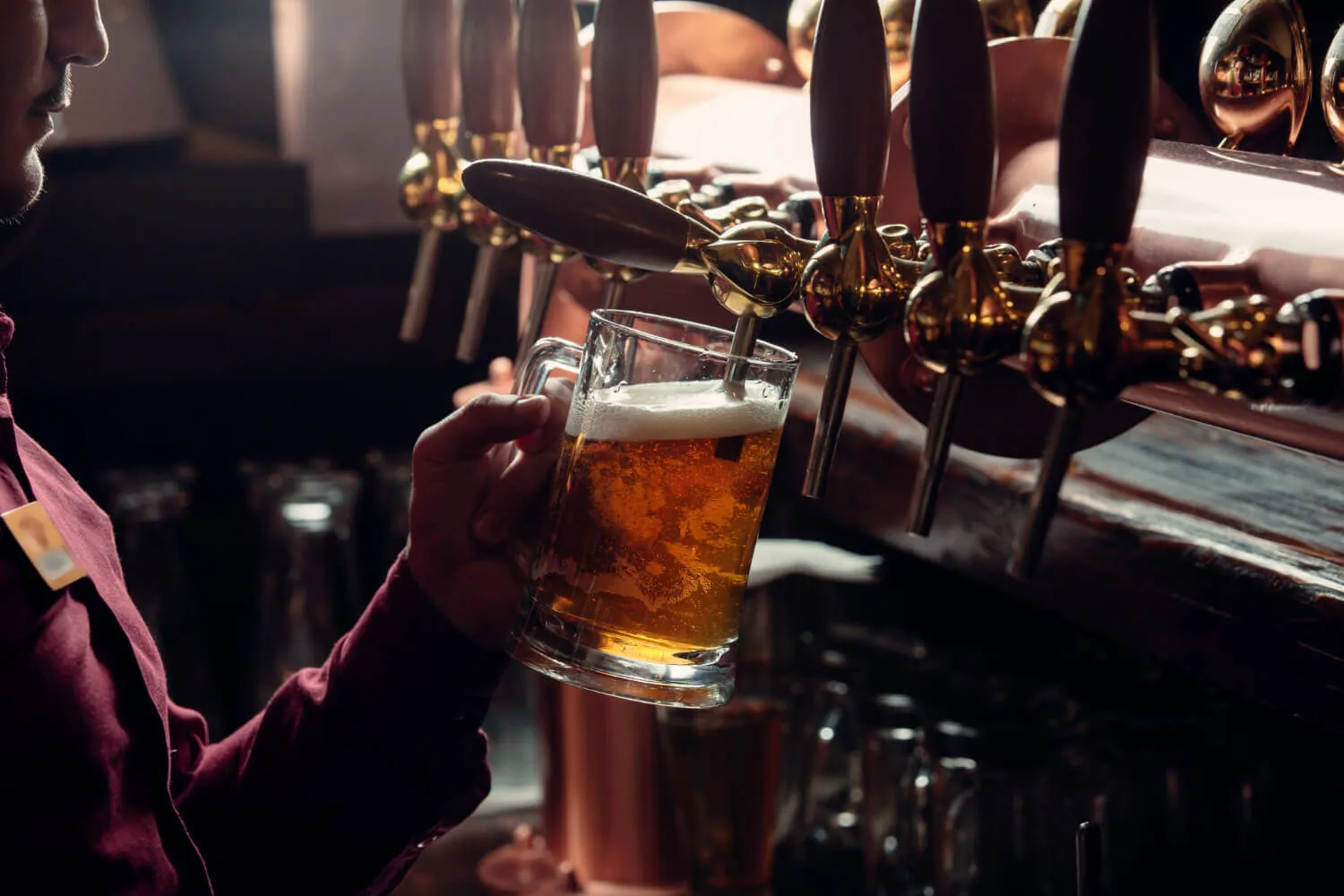
Choosing the correct beer line size is crucial for any draft beer system's performance. The beer line connects the keg to the faucet and its size can significantly impact the taste and quality of the beer dispensed. Typically measured in inches or millimeters, the inner diameter of the tubing must be properly selected to maintain a balance between the pressure and flow rate, ensuring that beer pours smoothly without excessive foam.
Finding the right balance in a beer dispensing system involves understanding the relationship between the length and inside diameter of the beer line, the type of beer being served, and the amount of pressure from the CO2 or nitrogen used to dispense the beer. A carefully calibrated beer line ensures that beer is delivered from keg to glass at the intended carbonation level with the right taste and aroma characteristics. For most home setups, a certain inside diameter is standard, but commercial setups or those with longer distances between the keg and tap may require different sizes to achieve the perfect pour.
Key Takeaways
- Proper beer line size is essential for optimal beer dispensing.
- Beer line balance affects taste, foam, and pour quality.
- Consider line length, diameter, and pressure for system calibration.
Understanding Beer Line Basics
A proper understanding of draft beer dispensing system and line systems is critical for achieving the perfect pour. The size, material, and components of the system all play pivotal roles in the functionality and quality of the draft beer dispensing system.
Components of a Beer Line System
A beer line system typically includes the tubing that carries beer from the keg to the faucet. Key components include the beer line (tubing) the kegs itself, couplers, fittings, regulators, separators/blenders and the faucet. The coupler attaches to the keg, and the regulator manages the pressure of the gas pushing the beer through one end of the tubing.
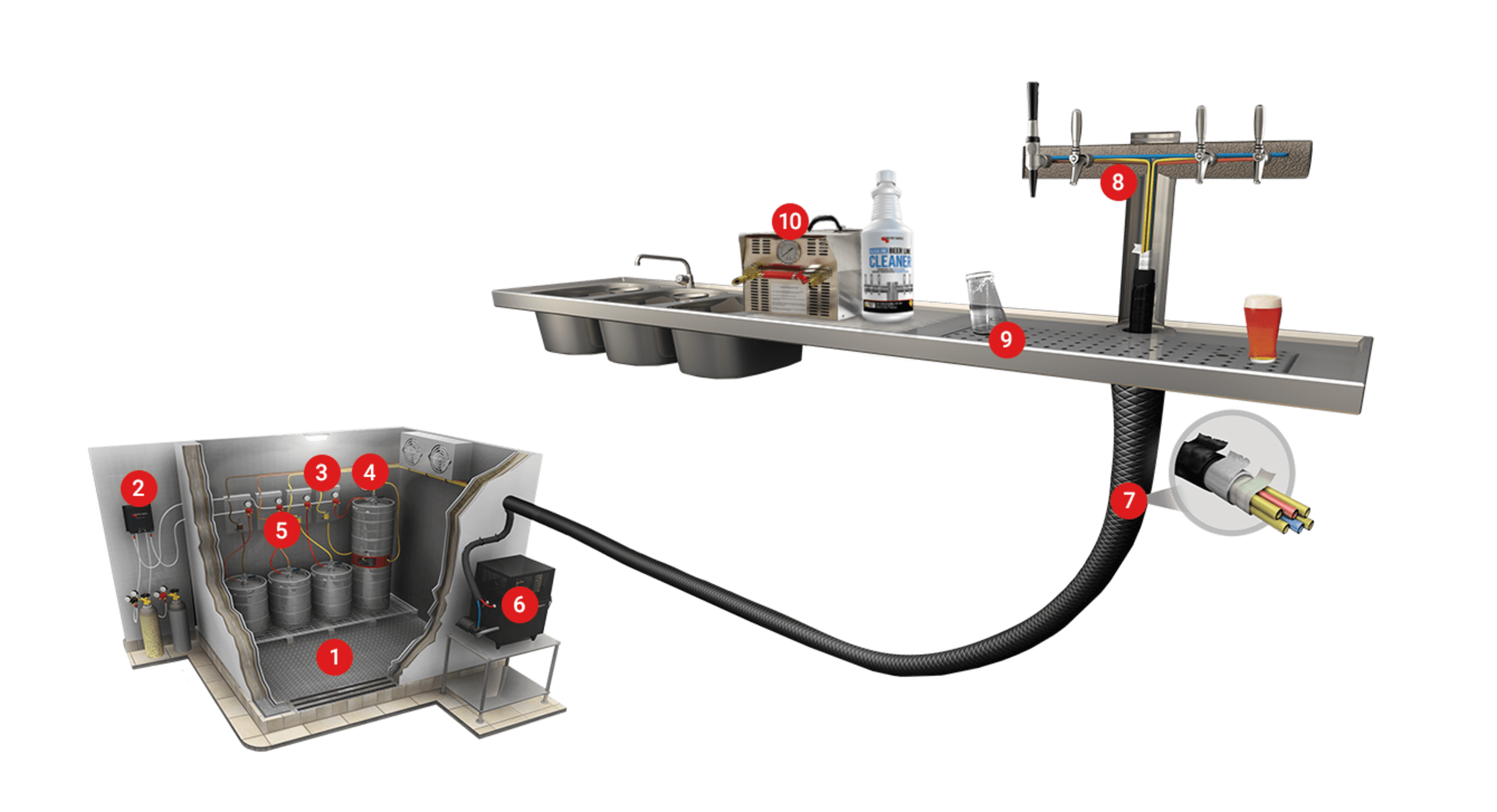
The Importance of Beer Line Diameter
The diameter of the beer line is crucial. It affects the resistance the beer encounters as it flows, which in turn impacts the pour and carbonation level. Interior diameter tubing (ID) specifications are usually in either millimeters or inches, with standard sizes being 5mm ID or 3/16″ ID. The length and diameter barrier tubing must balance to maintain correct dispensing pressure, with a common guideline being an 8 to 10 feet length for 3/16″ ID tubing to minimize foam and ensure a consistent pour.
Understanding the importance of the internal diameter (I.D.) of beer lines in a draft system is crucial for achieving a great pour. Here are the key reasons:
1. Flow Rate Control: The I.D. of the beer line significantly influences the flow rate of the beer. A smaller diameter results in a slower flow, while a larger diameter allows for a faster flow. The ideal flow rate for beer is typically around 2 ounces per second. If the flow is too fast, it can lead to excessive foaming; if too slow, it can result in flat beer.
2. Resistance and Balance: Beer lines provide resistance, which is necessary to balance the system. The length and diameter of the line contribute to this resistance. A system with too little resistance will pour beer too quickly, causing foam, while too much resistance can slow down the pour excessively. The right I.D. helps in achieving the correct balance between the pressure in the keg and the resistance in the line.
3. Foam Management: Proper foam control is essential for a good pour. The diameter of the beer line affects the amount of turbulence as the beer flows through it. If the line is too wide, the beer can become overly agitated, leading to excessive foam. Conversely, too narrow a line can restrict the flow, also resulting in poor foam quality.
The internal diameter of beer lines in a draft system is a key factor in controlling the flow rate, managing foam, balancing the system, and maintaining the quality and temperature of the beer. Getting it right is essential for a great pouring draft system.
Identifying the Right Beer Line Material
Micromatic's barrier tubing is often considered superior in the draft beer system industry for several reasons. These factors contribute to its reputation for quality and reliability:
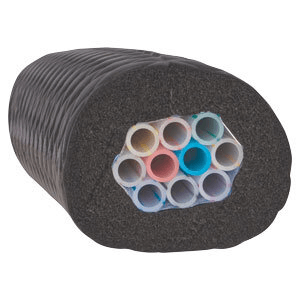
1. Advanced Material Composition: Micromatic barrier tubing is typically made from advanced materials that offer superior resistance to the permeation of oxygen and carbon dioxide. This is crucial for maintaining the freshness and flavor integrity of the beer over time, especially important in systems with long draw distances.
2. Flavor Preservation: The construction of the tubing is designed to ensure that the beer's flavor is not affected as it travels from the keg to the tap. This is a significant advantage over some other types of tubing that can impart a plastic taste to the beer or absorb flavors from previous batches.
3. Durability and Strength: The tubing is known for its durability and resistance to kinking and wear. This makes it a reliable choice for both commercial and home setups, where the lines may be subject to frequent use and movement.
4. Chemical Resistance: The material used in Micromatic's barrier tubing is resistant to the cleaning chemicals commonly used in the industry. This resistance ensures that the tubing's integrity is maintained over time, even with regular cleaning and sanitation processes.
5. Reduced Maintenance: Due to its resistance to flavor absorption and chemical damage, Micromatic's tubing often requires less frequent replacement than other types, reducing long-term maintenance costs and effort.
XtraFlexmaster Tubing
XtraFlexmaster® tubing stays clean for a really long time. When people tested it, they found that it had fewer germs after 5 weeks than vinyl tubing had after just 2 weeks. There's a special size of this tubing, 3/16 inches inside, that's perfect for when the beer keg and the tap are not too far apart, like less than 5 feet. This size is just right because it makes sure the beer doesn't come out too fast or too slow when it's pushed from the keg. This tubing is great for breweries because it doesn't get ruined, swell up, or dry out, even when you clean it with normal beer line cleaners. It's not too expensive, and you can buy just a little bit or a lot, whatever you need.
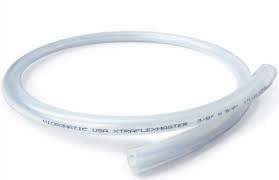
The Science of Draft Beer Flow
Achieving the perfect pour from a draft beer system involves understanding the flow rate and how it interacts with factors such as carbonation and resistance.
Factors Affecting Beer Flow Rate
The flow rate of beer from a keg through the tap is a critical aspect of draft beer systems, affecting both pour speed and quality. Several variables influence this rate, including pressure, the length and width of the beer line, and the level of carbonation in the beer itself.
- Pressure: The applied CO2 pressure is essential to propel beer through the lines, with higher pressure generally increasing flow rates.
- Beer Line Length: Extensive research on keg line balancing indicates that longer lines increase resistance, which can help to reduce foam but may require more pressure to maintain the optimal flow rate.
- Diameter: The internal diameter of the beer line also impacts resistance. For example, commercial setups may opt for a larger diameter, such as ⅜", to facilitate a quicker flow with less required pressure.
Carbonation and Resistance
Carbonation level, indicated by the amount of dissolved CO2, plays a crucial role in defining the resistance within the beer line, often contributing to the presence of foam in the poured beer.
- Carbonation: Higher levels of carbonation require careful balancing to avoid excessive foam. This demands precise pressure settings and an understanding of the right size beer line for maintaining the integrity of the beer's carbonation.
- Resistance: Every beer line material and setup offers a unique resistance factor, which needs to be calculated along with carbonation to determine the ideal pressure and flow rate. Tools like a beer line length calculator can assist in balancing these elements effectively.
By considering these factors and applying meticulous adjustments, one can achieve a consistent and ideal pour speed, minimizing foam and ensuring the beer served is as the brewer intended.
Optimizing Beer Line Length and Diameter
Optimal beer line length and diameter are crucial for maintaining the right carbonation and serving speed in a draught system. These factors ensure a perfect pour every time.
Calculating the Perfect Beer Line Length
The formula for beer line length is tailored to balance the pressure in a keg system, avoiding over-foamy or flat beer. To determine the correct length, one must account for the beer's applied pressure and the resistance created by the beer line. A commonly used equation is:
BL = (Ps - (RS x 0.5) - 1) / R
- BL = Beer line length (in feet)
- Ps = Pressure set on the regulator (PSI)
- Rs = Rise from keg to tap (feet)
- R = Resistance factor depending on the beer line diameter
This calculation ensures the beer is dispensed at the desired rate and helps in selecting a befitting beer line length for particular kegs or systems. A longer beer line may be needed for systems with higher elevation from the keg to the tap.
Choosing the Optimal Beer Line Diameter
Selecting the optimal beer line diameter can impact resistance and the rate at which beer flows. Standard beer line sizes typically range between 3/16-inch to 3/8-inch. The smaller the diameter, the greater the resistance; thus, it requires higher pressure to dispense beer properly. Conversely, a larger diameter reduces resistance and may require shorter lines. Here's a precise look at common beer line sizes:
- 3/16-inch (I.D.): Provides high resistance; good for systems with shorter runs.
- 1/4-inch (I.D.): A middle-ground option for moderate resistance.
- 3/8-inch (I.D.): Offers less resistance; suitable for longer beer lines.
The choice depends on factors such as the desired flow rate and the specific beer being served. Properly balancing beer line length and diameter helps achieve a perfect pour and preserve the taste quality of the beer.
Balancing Your Draft System
To achieve the perfect pour, understanding and adjusting two key aspects of your draft system are crucial: the pressure settings and the beer's carbonation levels. Each beer style comes with its own required balance in the system to maintain the right carbonation and serving pressure.
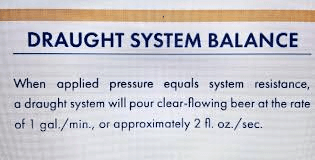
Pressure Settings and Carbonation Levels
The keg pressure or CO2 pressure is pivotal in dispensing beer. The gas pressure applied from the CO2 tank must match the carbonation level of the beer to avoid over-foaming or under-carbonation. A general rule is that the serving pressure should be the same as the carbonation level of the beverage. If the system balancing is off, it can lead to either too much foam or a flat beer.
- To calculate the ideal pressure:
- Serving Pressure (psi) = Amount of CO2 required (volumes) + Temperature Factor + Elevation Factor
- Factors affecting pressure:
- Temperature of Beer: Colder beer can hold more CO2.
- Height Difference between the keg and the tap: Gravity affects flow rate.
The Role of Beer Style in System Balance
The beer style greatly influences system balance. Different beers demand specific carbonation levels, most beers which require adjustments in the pressure settings. For example, a stout may require a lower carbonation level, hence lower serving pressure, compared to a highly carbonated pilsner.
- Carbonation levels by beer style:
- Stouts and porters: Typically lower carbonation (1.6-2.0 volumes of CO2).
- Ales and lagers: Moderate carbonation (2.2-2.7 volumes of CO2).
- Wheat beers and Belgian ales: Higher carbonation (2.7-4.5 volumes of CO2).
It's essential to tailor the serving pressure to the type of beer to serve to preserve its character and ensure a perfect tasting experience.
Troubleshooting Common Draft Beer Issues
In draft beer systems, two prevalent issues are excessive foaming and slow pours. Addressing these concerns effectively requires a methodical approach to identify and resolve the underlying causes.
Dealing with Excessive Foaming
Excessive foaming can mar the draft line and beer experience and lead to waste. Temperature is a critical factor; beer should be stored and dispensed between 36-38°F. If the beer is too warm, it will foam excessively. Checking the CO2 pressure is also paramount—it should be set properly, usually between 12-14 PSI for ales and lagers. A detailed troubleshooting guide can help diagnose and fix issues leading to excessive foaming. Lines should be free of kinks and of the proper diameter and length to maintain optimal resistance.
Addressing Slow Pours
Slow pours can frustrate customers and disrupt service. The issue is often caused by an obstruction in the lines or a need for increased pressure. Beer lines should be inspected regularly for any blockages or kinks. Additionally, the applied pressure might need adjustment; it can be too low for the system's demands. A comprehensive understanding of beer line dynamics can prevent slow pours and ensure consistent, quality service. Maintaining the correct temperature and CO2 pressure is also necessary to avoid slow or foamy pours.
Advanced Beer Line Concepts
In advanced draft beer dispensing systems, the precision of beer line size and the understanding of gas blends play critical roles in maintaining the quality and consistency of the draft beer experience.
Long-Draw Systems and Trunk Lines
In a long-draw system, beer must travel a considerable distance from the keg to the tap, which introduces a range of complexities. An optimal trunk line—typically insulated bundling of beer and coolant lines—must balance diameter and length to ensure the beer’s quality. For instance, a 3/8" (95 mm) I.D beer line helps to mitigate resistance over long distances, facilitating a smoother flow to the tap.
Example of trunk line size selection:
Inside Diameter (I.D) Recommended Length 5/16" (79 mm) Shorter distances 3/8" (95 mm) Longer distances
Although larger diameters and larger tubing may reduce resistance, a professional must consider the beer line size for long draw systems carefully to prevent excessive beer flow that can lead to foaming.
Understanding Gas Blends in Draft Beer
The gas blend used in a draft beer system, often referred to as beer gas, is crucial for perfecting the pour. Nitrogen is commonly blended with carbon dioxide to create a suitable gas mix that provides the proper pressure and minimizes the risk of over-carbonation. This is especially important for certain beer styles requiring a smooth, creamy head, as served in a traditional stout.
Table of gas blend impact:
Gas Mix Impact on Beer CO2 Crispness, carbonation level Nitrogen/CO2 Blend (Beer Gas) Creamier texture, reduced carbonation
Professionals must accurately determine the balance in their gas blends for draft beer to align with the desired beer characteristics while maintaining an efficient and trouble-free dispensing system.
Maintaining and Cleaning Beer Lines
Ensuring the quality of beer service requires meticulous maintenance routines, especially when it comes to the beer lines. Proper cleaning protocols can prevent clogs and preserve the beer's intended taste and aroma.
Regular Cleaning to Prevent Clogs
Frequency: Experts recommend cleaning beer lines every two weeks to prevent the buildup of organic materials and mineral deposits that can lead to clogs. This routine should include:
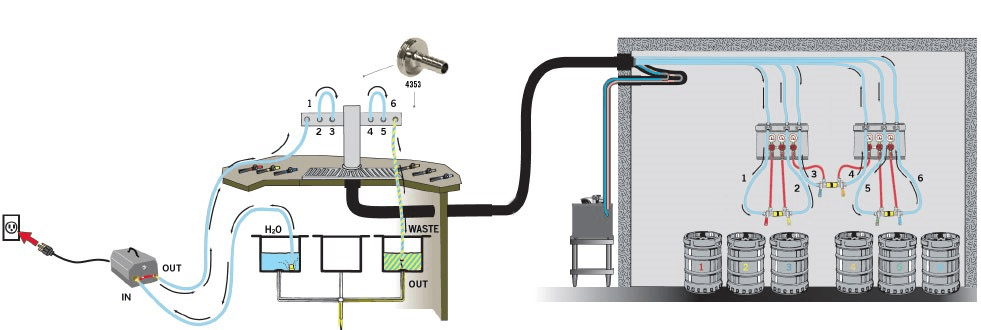
- Agitation: Utilizing a cleaning solution to scrub the internal surfaces.
- Flushing: Thoroughly rinsing the lines with clean water post-cleaning to remove any residual cleaner.
By adhering to this schedule, establishments prevent clogs, ensuring a smoother delivery of beer from keg to tap.
The Impact of Cleanliness on Taste and Aroma
Chemical Contact: The type of cleaning solutions should be carefully chosen (typically a mix of sodium or potassium hydroxide), and they must make contact with the beer lines for the recommended duration. This process is crucial for eliminating contaminants that can taint taste and aroma.
Sensory Quality: A clean beer line ensures that the beer served is true to its intended flavor profile, without off-flavors or odors that can result from bacterial growth or yeast build-up. Regular maintenance preserves the aroma and taste that brewers work hard to perfect.
Commercial Draft Beer System Insights
In the realm of commercial draft beer systems, precision in design and efficiency is paramount. For establishments seeking to deliver the perfect pour, understanding the technical intricacies of these systems is critical.
System Design for Commercial Environments
Commercial systems cater to a high volume of customers, requiring a robust and carefully planned layout to maintain consistent beer quality and seamless delivery. Beer Towers play a role in this setup, serving as the central fixture for dispensing multiple beers. When considering system design for commercial environments, attention must be paid to the beer line size to ensure a proper balance between pressure and resistance, which directly affects the beer's mouthfeel and carbonation level.
Summary
In choosing the correct beer line size for a beer system, one must consider the inner diameter and the length of the tubing. The inner diameter affects the flow rate and resistance, which in turn influences the amount of foam produced when pouring a beer.
- Standard Sizes: Beer lines commonly range in internal diameter (ID) from 3/16 inch to 3/8 inch.
- Flow Rate: A larger diameter can facilitate a quicker flow rate, which is crucial in commercial settings where speed is important.
One should adjust the beer line length depending on the pressure output of the beer system to ensure the right balance between resistance and delivery. If the line is too short or the head diameter too large for the pressure applied to cleaning keg itself, the beer may pour too quickly, resulting in excess foam. Conversely, a line that is too long or too narrow can slow down the pour excessively.
Selecting the appropriate beer line size is imperative for achieving the perfect pour. It requires understanding the relationship between the length, diameter, and pressure within the system.
For any questions please reach out to us at Rennys Draft Solutions.